What are car brake rotors made of? Car brake rotors are a crucial component of the braking system, playing a vital role in vehicle safety by helping to stop the car efficiently. These rotors, also known as brake discs, are made from various materials, each offering distinct advantages and characteristics.
Understanding what car brake rotors are made of can help you make informed decisions when it comes to maintenance, replacements, and performance upgrades. In this blog post, we will explore the different materials used to make brake rotors, their benefits, and their applications.
Understanding to Brake Rotors
Brake rotors are part of a disc brake system, which is commonly used in modern vehicles due to its superior stopping power and heat dissipation compared to drum brakes. When you apply the brakes, the brake pads clamp down on the rotors, creating friction that slows down the wheel rotation and ultimately brings the vehicle to a stop. The effectiveness of this process heavily relies on the material composition of the brake rotors.
Common Materials Used for Brake Rotors
- Cast Iron
- Steel
- Carbon Composite
- Ceramic
- Aluminum
Each of these materials has unique properties that make them suitable for specific applications, ranging from everyday driving to high-performance racing.
Cast Iron Brake Rotors
Composition and Characteristics
Cast iron is the most commonly used material for brake rotors, particularly in standard passenger vehicles. Cast iron rotors are made from a mixture of iron, carbon, and silicon, providing a good balance of strength, durability, and heat dissipation.
Advantages
- Durability: Cast iron is highly durable and can withstand the high temperatures generated during braking.
- Heat Dissipation: It has excellent thermal conductivity, which helps to dissipate heat quickly and prevent brake fade.
- Cost-Effective: Cast iron rotors are relatively inexpensive to produce, making them a cost-effective option for most drivers.
Disadvantages
- Weight: Cast iron rotors are heavy, which can affect the overall weight of the vehicle and its fuel efficiency.
- Corrosion: They are prone to rust and corrosion, especially in humid or salty environments.
Applications
Cast iron rotors are commonly used in everyday passenger vehicles, light trucks, and SUVs. They provide reliable performance for typical driving conditions.
Steel Brake Rotors
Composition and Characteristics
Steel brake rotors are made from a combination of iron and carbon, similar to cast iron, but with additional alloying elements to improve strength and resistance to wear.
Advantages
- Strength: Steel rotors are stronger and more resistant to wear than cast iron rotors.
- Weight: They are lighter than cast iron rotors, which can improve vehicle performance and fuel efficiency.
Disadvantages
- Cost: Steel rotors are generally more expensive than cast iron rotors.
- Heat Management: They may not dissipate heat as effectively as cast iron rotors, which can lead to higher temperatures and potential brake fade under extreme conditions.
Applications
Steel rotors are often used in performance vehicles and sports cars where weight savings and strength are critical.
Carbon Composite Brake Rotors
Composition and Characteristics
Carbon composite brake rotors are made from a combination of carbon fibers and resin, often reinforced with ceramics. These materials create a rotor that is both lightweight and extremely strong.
Advantages
- Lightweight: Carbon composite rotors are significantly lighter than both cast iron and steel rotors, reducing unsprung weight and improving vehicle handling and performance.
- Heat Resistance: They can withstand extremely high temperatures without losing performance, making them ideal for high-performance and racing applications.
- Durability: Carbon composite rotors are highly resistant to wear and have a long lifespan.
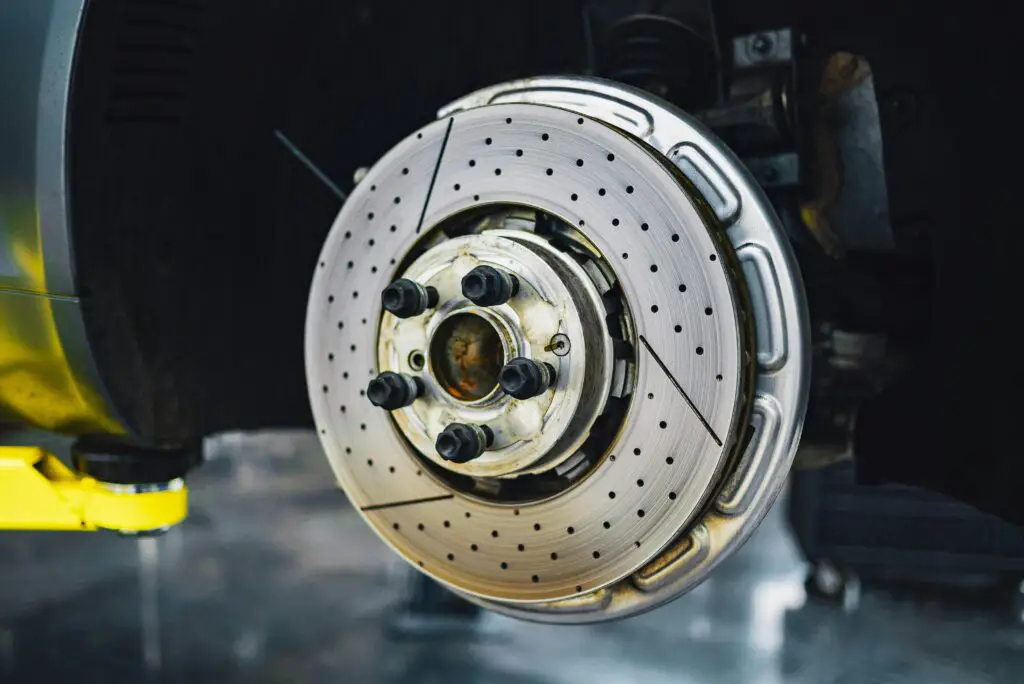
Disadvantages
- Cost: These rotors are very expensive to produce, making them less accessible for the average driver.
- Noise and Vibration: They can generate more noise and vibration compared to other materials, which might be undesirable for everyday driving.
Applications
Carbon composite rotors are primarily used in high-performance sports cars, racing cars, and some high-end luxury vehicles where maximum performance is a priority.
Ceramic Brake Rotors
Composition and Characteristics
Ceramic brake rotors are made from a mixture of ceramic materials and copper fibers. This composition creates a rotor that is both lightweight and capable of withstanding high temperatures.
Advantages
- Heat Management: Ceramic rotors have excellent heat dissipation properties, reducing the risk of brake fade.
- Durability: They are resistant to wear and can last longer than traditional metal rotors.
- Quiet Operation: Ceramic rotors tend to produce less noise and vibration compared to metal rotors.
Disadvantages
- Cost: Like carbon composite rotors, ceramic rotors are expensive to manufacture.
- Performance: While they are excellent for heat management, they may not provide the same level of initial bite as some high-performance metal rotors.
Applications
Ceramic rotors are often used in high-performance and luxury vehicles, as well as in some electric and hybrid cars where reduced weight and noise are important.
Aluminum Brake Rotors
Composition and Characteristics
Aluminum brake rotors are typically made from an aluminum alloy combined with other metals to enhance strength and heat resistance. They are sometimes used in combination with a ceramic coating to improve performance.
Advantages
- Lightweight: Aluminum rotors are lighter than cast iron and steel, improving fuel efficiency and handling.
- Corrosion Resistance: They are highly resistant to corrosion, making them ideal for use in harsh environments.
- Heat Dissipation: Aluminum has excellent thermal conductivity, helping to dissipate heat quickly.
Disadvantages
- Strength: Aluminum rotors may not be as strong or durable as cast iron or steel, which can limit their use in high-stress applications.
- Cost: They can be more expensive than traditional cast iron rotors.
Applications
Aluminum rotors are often used in performance vehicles, motorcycles, and electric vehicles where weight savings and corrosion resistance are crucial.
Choosing the Right Brake Rotors
When it comes to choosing the right brake rotors for your vehicle, consider the following factors:
- Driving Conditions: For everyday driving, cast iron or steel rotors are usually sufficient. If you frequently drive in harsh conditions or participate in performance driving, you may benefit from ceramic or carbon composite rotors.
- Budget: Cast iron rotors are the most cost-effective, while ceramic and carbon composite rotors can be significantly more expensive.
- Vehicle Type: The type of vehicle you drive can influence your choice. Performance cars and motorcycles may benefit from lightweight materials like aluminum or carbon composites, while trucks and SUVs might need the durability of cast iron.
- Maintenance: Consider the maintenance requirements and longevity of the rotors. High-performance materials often require less frequent replacements but can be more costly upfront.
Conclusion
Car brake rotors are typically made from cast iron, steel, carbon composite, ceramic, or aluminum, each offering unique benefits. Cast iron rotors are durable and cost-effective, commonly used in everyday vehicles. Steel rotors provide strength and weight savings, ideal for performance cars.
Carbon composite and ceramic rotors excel in high-performance applications due to their lightweight and superior heat resistance but come at a higher cost. Aluminum rotors, known for their corrosion resistance and light weight, are often used in performance and electric vehicles. Choosing the right material depends on driving conditions, vehicle type, and budget.
Discover more from Chikwem
Subscribe to get the latest posts sent to your email.